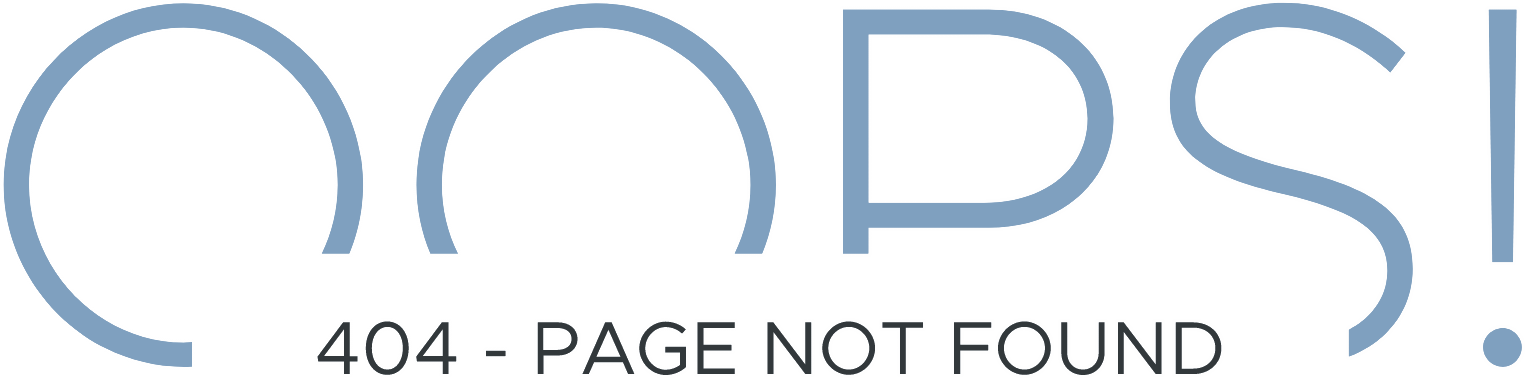
Looks like this page is still busy unloading at goods receipt! Don’t let your warehouse get stuck in the same jam — discover the powerful solutions offered by our PROLAG World warehouse management software. Smooth operations, guaranteed (no forklift required)!